Chlorinated Polyvinyl Chloride Pipes (CPVC)
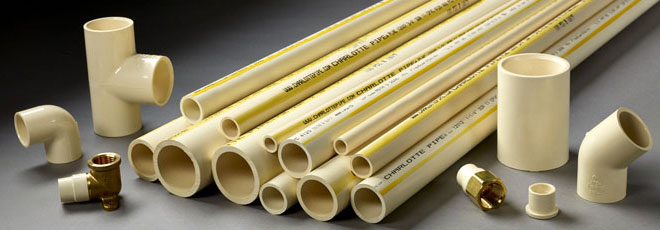
CPVC tubing comes in nominal sizes ranging from 1/2 to 2 in. copper tube size (CTS), and pipe sizes ranging from 1/2 to 24 in. (Sch 40/80) iron pipe size (IPS). CPVC tubing is SDR11 (1/2 to 2 in.) with standard hydrostatic pressure ratings of 400 psi at 73ºF (2,750 kPa at 23ºC) and 100 psi at 180ºF (690 kPa at 82ºC). Consult the specific CPVC pipe manufacturer’s literature and listings for appropriate pressure ratings. CPVC tubing and pipe are sold in straight lengths.
Definition
PVC (polyvinyl chloride) that has been chlorinated via a free radical chlorination reaction. CPVC is produced by adding chlorine to PVC in a water slurry or fluidized bed chlorination process. The chlorination reaction is initiated by ultraviolet light. The chlorinated PVC is compounded with ingredients necessary for the desired properties for further processing. The chlorine added to PVC gives CPVC higher temperature performance and improved fire and corrosion resistance.
Overview
CPVC is a high-temperature plastic pressure piping system introduced for potable plumbing in 1959. It has also been used extensively in fire sprinkler systems since 1985. This material is also used for many industrial and process piping applications. CPVC pipe is available in nominal sizes from 1/2″ to 24″ and is approved in all model plumbing and mechanical codes across the United States and Canada. In addition, CPVC pipe and fittings from select manufacturers are listed for light hazard fire sprinkler systems, as defined in NFPA 13, 13R and 13D standards.
CPVC Advantages
- Safety of potable water and long-term reliability
- Resistance to corrosion, tuberculation, deposits
- Chlorine and chloramine resistance
- Lightweight, easy to transport
- Available in wide range of sizes
- Noise and water hammer resistance
- No scrap value, avoiding jobsite theft
- Durability and toughness to survive jobsite installations
- No flame used for joining, solvent cement joints
- Universal compatibility of pipes/fittings
- Professional installed appearance
CPVC Applications
- Hot and cold water plumbing distribution, residential and commercial
- Fire protection: One- and Two-Family Dwellings and Manufactured Homes (NFPA 13D), Low-Rise Residential Occupancies (NFPA 13R) and Light Hazard Occupancies (NFPA 13)
- Reclaimed water piping (purple pipe)
- Chilled water piping
- Hydronic piping and distribution (radiators, fan coils, etc.)
- Suitable for many industrial and process piping applications
Copper Water Pipes
Copper pipe is mostly used for hot and cold water distribution, as well as being regularly used in HVAC systems for refrigerant lines. Although once used in gas piping, this is no longer allowed in most jurisdictions. Copper piping works in both underground and above-ground applications, but copper can be affected by some soils and it should have a protective sleeve if used underground.
For many years, copper was the gold standard for water supply pipes, as galvanized steel fell from favor. Copper plumbing pipes can last for up to 50 years, but as it ages, copper thins out, eventually leading to pinhole leaks. More recently, various forms of plastic have replaced copper as the favorite, though copper pipes and fittings are still widely available. Due to the price of copper and the longer labor needed to install, many builders have switched to alternative water distribution piping, especially PEX.
Copper comes in different thicknesses which are labeled M, L, and K. M is the thinnest grade of copper. Copper can be connected in different ways, including compression fittings, push-fit fittings, or sweat-soldering.
Galvanized Water Pipes
If you live in a home built before 1960, chances are your plumbing system is made of galvanized steel or iron pipes. Galvanized pipes were the standard in homebuilding for decades, but times have changed, and many homeowners are making the switch to alternatives like copper.
But do you really need to worry about galvanized pipes? In this article, we’ll get into a little background on these older pipes and talk about what they mean for the health of your home and its plumbing system. If you happen to have galvanized pipes in your home, we’ll give you our two cents on how best to proceed — whether you should stick with them or have them replaced.
What Are Galvanized Pipes?
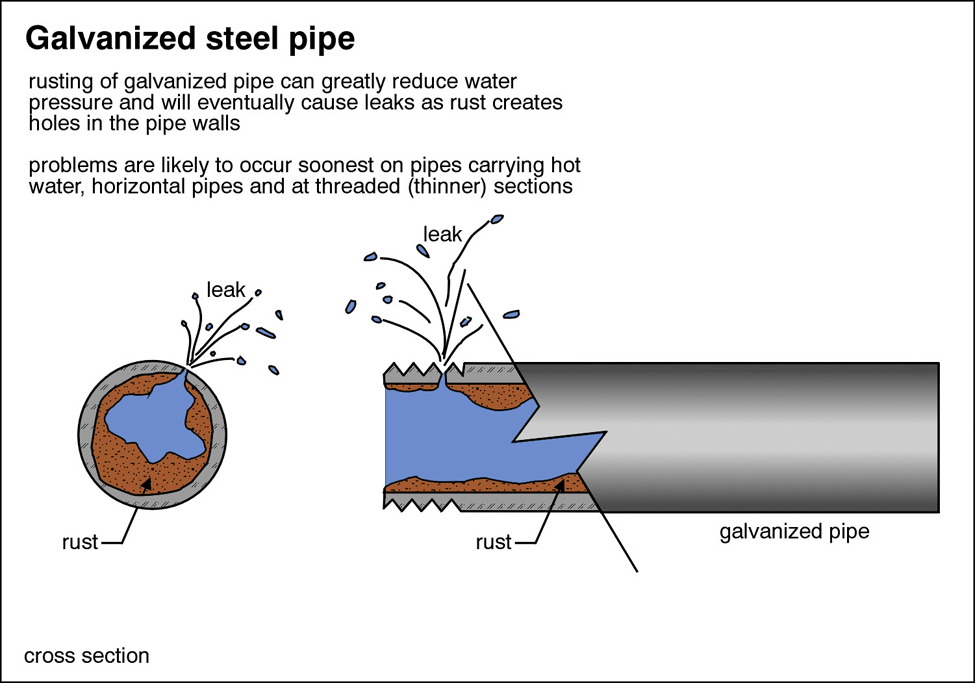
For most of the modern era, lead pipes were used when building plumbing systems (yes, even for drinking water). Thankfully, we eventually realized that lead pipes are a giant public safety hazard. So lead pipes were out, and we needed a new material. Iron and steel were perfectly good alternatives, except for one little snag; both iron and steel rusts over time.
Enter galvanization. By coating iron and steel in a protective layer of zinc, pipes had a buffer zone against the elements. Starting around 1960, these galvanized pipes became the staple in homes all around the world. Unfortunately, it wasn’t exactly a perfect solution, as you’ll soon learn.
As time went on, it became clear that there were some problems with galvanized pipes. While a freshly installed network of galvanized steel plumbing typically works without a hitch, after 30 or 40 years, a few issues start to pop up:
- Rust buildup. Galvanized pipes are often victims of corrosion and rust over time. Galvanization doesn’t stop rust, it just creates a new layer on the pipe that is exposed to rust first. But as years and decades go by, the protective zinc layer eventually becomes completely corroded.
- Low pressure and leaks. Homes with galvanized pipes can eventually suffer problems with water pressure and even leaks or pipe bursts. Pipe leaks often occur at the pipe joints — typically behind walls — where the buildup of water and moisture can go unnoticed for long periods of time. Which could mean eventual structural damage, toxic mold, and expensive repairs.
- Potential health risks. The zinc layer in galvanized pipes often contains impurities like lead or other heavy metals. Lab tests have found that galvanized pipes can have up to 10 times the amount of lead deemed hazardous by the Environmental Protection Agency. Once corrosion sets in, these contaminants can work their way into your drinking water, which is a problem you don’t want to have.
- Rust colored water. Once the interior of galvanized pipes has been corroded enough, iron can get into the water, giving it a rusty brown color.
As you can see, having a galvanized steel plumbing system is a bit of a ticking time bomb. And if you live in an older home, there’s a pretty good chance your plumbing network is using this outdated material. But how can you know for sure?
Do I Have Galvanized Pipes?
You don’t have to go digging through building records to determine if your home has galvanized pipes. Just find an area of exposed pipe and scratch it with a nickel or screwdriver to reveal its true color. Use a strong magnet; if it sticks it’s likely galvanized pipe If it looks like a penny, you have copper piping. If it looks metallic gray, you probably have galvanized steel or iron pipes.
Should Galvanized Pipes Be Replaced?
The short answer is yes, you should definitely look into an upgrade if your home is outfitted with galvanized pipes. Replacing your old pipes with new copper pipes might be an expensive job, but it can save you a ton of money in the long run. However, if your pipes seem to be in a good state currently and you aren’t planning on living in your home for several decades, you might be fine with just a little minor maintenance.
The first thing you have to consider is money saved on future repairs. Since we know that galvanized pipes break down over time, replacing them can significantly lower your chances of expensive leaks, pipe bursts and water damage.
Water damage that builds up over time can lead to some serious repair bills. And the small, undetected leaks that cause invisible water damage also waste hundreds, even thousands of gallons of water every year, costing you even more on your utility bills.
Getting Smart About Plumbing
- Upgrade your plumbing network with modern, copper pipes. In addition to being resilient to rust and corrosion, copper pipes don’t pose a risk for lead or other nasty substances. A brand-new copper plumbing system can last up to 75 years.
- Learn about different ways to maintain healthy plumbing in your home. Winterizing your pipes, learning how to deal with clogs, and taking care of your garbage disposal can save you a ton of money in the long run. Small changes can lead to huge benefits.
- Use a smart home water security system like Flo by Moen. Its Smart Water Shutoff proactively monitors your home’s water pressure and flow, as well as ambient temperature, to detect even the smallest microleak. And all that information is sent directly to your smartphone, so you can check up on the state of your plumbing wherever you are. If your pipe bursts, it is even smart enough to shut off your home’s water in order to protect it from serious damage.
- In the current landscape of plumbing technology, galvanized pipes are slowly becoming a thing of the past. New constructions virtually never use them. If you’re looking at ways to make your home last far, far into the future, replacing your old plumbing network should make its way to your to-do list.
Orangeburg Waste Pipes
What is Orangeburg Pipe? Everything You Need to Know
Posted by William Heinselman on Feb 17 2020
What is Orangeburg Pipe?
Orangeburg pipe is a type of home sewer pipe used in many properties built from 1945 to 1972. Also known as “no-corrode” pipe, Orangeburg is a type of bituminized fiber pipe made from a mixture of hot pitch and wood pulp. It gets its name from Orangeburg, New York, where it was originally mass-produced by the Fiber Conduit Company (which later changed its name to the Orangeburg Manufacturing Company).
Although various forms of bituminized fiber pipe have been used since the 1800s, Orangeburg owes its origins to World War II, when the iron and steel commonly used for sewer pipes were critical to the war effort. Because of these shortages, Orangeburg pipe was invented so more iron and steel could go toward producing war materials. Following the war, Orangeburg continued to proliferate because it was cheap.
Once installed, standard Orangeburg sewer pipes were expected to last 50 years’ time. Unfortunately, many systems began to falter after a mere 30 years of use. Most of these structural complications resulted from the material used to manufacture the pipe. Essentially, Orangeburg pipe is little more than asphalt-soaked paper and pulp. It may seem obvious in retrospect, but if you soak paper (even tar paper) with water for long enough, it will eventually deform. Combined with the pressure from the soil above the pipe, it’s not surprising these pipes began to fail so quickly.
Problems With Orangeburg Sewer Pipe
In contrast to piping made from cast iron or clay, Orangeburg pipes absorb moisture and become distorted, oftentimes in an ovular shape, under pressure. Layers of this material are also subject to bubbling up and closing the pipe off. Often described by plumbing professionals as nothing more than a “coal tar-impregnated toilet paper tube,” it’s something of a miracle that many Orangeburg pipes have lasted as long as they have.
Typically made with diameters between 2 and 18 inches, Orangeburg fell out of popularity in the early 1970s, as more reliable, efficiently produced pipe materials became available. As they were the primary option for low-cost sewer pipes until that time, Orangeburg pipe sewer systems are still featured in many older homes. For most homes built using Orangeburg, the piping has likely either already deteriorated or is on the verge of collapse. Homeowners who do not inspect and measure the deterioration of their Orangeburg systems may be faced with large-scale replacements and severe damage in time. If ignored, they could result in an extremely messy and extremely expensive sewer line collapse.
Orangeburg Pipes and Your Home
To assess the presence of Orangeburg pipes in your home, typically, homeowners need to only know the age of their home and approximate year of pipe installation. In almost any home built between the years 1945 and 1972, Orangeburg pipe systems will comprise that property’s sewage system. Additionally, landlords, real estate records and city documents will typically have this information on file.
When the deterioration of Orangeburg pipelines begins, property owners may notice the service and efficiency of their home’s sewer system and other piping change; this is the sewage system starting to fail. If this problem is left uncorrected, it can threaten the safety and health of home inhabitants.
First and foremost, if you’re buying a home that was built before 1980, have a professional plumber do an inspection to ensure there’s not Orangeburg piping (if there is, you can subtract the replacement estimate from your offer). If you’re already settled and are unsure whether you have Orangeburg piping, the previous homeowner or city documents may have the answer; if not, it’s best to bring in a professional plumber who can do an inspection for you.
Signs of Orangeburg Pipe Failure
Homeowners of properties with Orangeburg pipelines may begin to notice poor pipe flow, decreasing efficiency and other service changes over time. This gradual decline in quality, often overlooked, can develop into larger, more expensive and severe pipe collapses. By knowing common signs and indicators of deterioration, homeowners can detect pipe damage earlier and avoid major, costly renovations.
If you notice any of the following indicators of Orangeburg pipe failure, it may be time to call a professional plumbing expert in your community to assess damages:
- Frequent or persistent blockages
- Decreased flows and water pressure
- Indentations and dampness on lawns
- Lush grass concentrations
- Progressing or sudden pipe collapse
- Tree root/biological penetration into pipelines
- Frequent toilet back-ups
- Foul sewer odors inside the home
- Mold issues
- Sinkholes in the foundation
- Sudden high spikes in your monthly water bill
Each case of Orangeburg pipe systems is different. While leaks, small breaks, and deteriorated surface areas can be reinforced with trenchless technologies, a full pipe replacement with PVC piping may be necessary if the Orangeburg pipe is too far deteriorated or unsalvageable. To avoid such a costly and property-damaging scenario, it is very beneficial for homeowners to get a professional inspection of their pipe system and repair deterioration while still possible.
Orangeburg Repair Solutions
The right solution for your broken Orangeburg pipe depends on a few key factors, which change based on circumstance. Things like pipe depth, the type of break, and the severity of the break all affect what solution is best suited for your home. To evaluate pipe systems, service professionals typically use video inspection technology to determine the source of performance problems; these methods are incredibly helpful in pinpointing deteriorated areas and estimating damage severity. Once the damage has been assessed, there are a few options available for repair.
The Traditional Dig-and-Replace Method
In conventional Orangeburg pipe renovations, the damaged pipes in question would have to be manually excavated and replaced with entire new segments of pipe. While this is fine for shallow pipelines (such as those less than 1-2’ below the yard surface), it can become tricky, and pricey, with increased depth or when surface-level fixtures (driveways, sidewalks, etc.) are involved. Often, the most expensive component of traditional pipe repairs isn’t the repair itself, but the remedial landscaping tasks, lawn damage and heavy labor that is typically required.
The bottom line: dig-and-replace pipe repairs are well-suited for shallow Orangeburg pipelines, or for pipe replacements in which bursting or other non-invasive techniques could prove problematic. Traditional repairs cost anywhere from $50-250 per foot of pipe, with a project average between $4,000-13,000.
Modern Trenchless Solutions: Pipe Lining
For situations where Orangeburg pipe runs below driveways, sidewalks or other fixtures, or is fairly deep underground, dig-free pipe lining can be an affordable alternative to manual dig-and-replace repairs. Completed via application of epoxy-resin liners within existing pipe (hence the industry term, “cured-in-place pipe”), these repairs often take a matter of hours, and eliminate days, if not weeks, worth of unnecessary labor.
Trenchless technology, a method of cured-in-place pipe lining (CIPP), can effectively repair moderate pipe deterioration and damages using a fiberglass and resin Perma-liner (which molds into PVC), epoxy coating and air pressure. Today, trenchless pipe lining has become a preferred method for renovating Orangeburg pipe systems, primarily due to its seamless application and incredible efficiency.
The process is simple: A Perma-liner solution is run through damaged, targeted pipe lines, and then pressed along the existing pipe walls using an air pressure bladder. This controlled pressure forces the liner into pipe cracks, fissures and breakages, and creates virtually flawless inner walls. Ideal for Orangeburg pipe repair situations, trenchless methods can also:
- Fill entire missing segments of pipe
- Smooth pipe offsets
- Fill large cracks and seal joint connections
- Reinforce Orangeburg pipe to last for 50+ more years
- Restore cracks, root damage, and broken pipes to a new condition
CIPP lining removes stress from your existing, damaged Orangeburg pipelines and places it on the new, precisely molded PVC pipe. This vastly improves the structural integrity of your pipe system and can boost pipe life expectancy by up to 50 years. The greatest advantage of trenchless methods over other repair options, however, is its minimal effects on your property and your wallet.
Trenchless renovations do not require large-scale digging or property damage, as they are completed with existing pipelines and often use existing pipe openings. Typically, the only digging done when using trenchless technology is for two small entry and exit holes, dug at both ends of the damaged pipe. This application, also safer and ‘greener’ than full excavation replacement, can be completed in a matter of hours, often done in a single day.
It’s because of this incredible efficiency and effectiveness that trenchless technology has been embraced by homeowners and service professionals alike for Orangeburg pipe repairs. As all cases of pipe deterioration and damage are different, it is important for homeowners to accurately assess the state of their pipelines before choosing a repair method.
Pipe lining’s effectiveness depends mainly on how severe the damage is to your Orangeburg pipe. If your Orangeburg pipe is collapsed, lining won’t do much to fix the problem. The pipe is still rigid enough to hold its shape and therefore the lining would make the structure strong but the flow would still be restricted. That’s a solution, but not a good one. If the problem is because the pipe is collapsed, you’ll have to replace the pipe.
Modern Trenchless Solutions: Pipe Bursting
If the breakage is significant or widespread throughout your pipe, another trenchless solution, pipe bursting, might be the answer. Pipe bursting is a trenchless alternative to manual pipe replacement, in situations where lining the existing pipe would not restore damages fully; this is often the case for collapsed, deteriorated Orangeburg pipe.
Using steel, conical bursting heads, which are attached to new pipes, trenchless specialists can replace your collapsed pipe entirely, without digging out the entire pipe. The cone bursting head fractures and displaces the old pipe, while simultaneously laying in place new pipe, all through small entry and exit points; this preserves both your yard and your wallet, and is the most efficient way to fully replace severely damaged pipe.
The bottom line: trenchless pipe lining can cost significantly less than dig-and-replace Orangeburg repair, as landscaping and extraneous labor tasks are largely avoided. Orangeburg pipe lining costs roughly $160 per foot, and can result in a mere $3,000 to $4,000 for small- to moderate-sized projects. Non-invasive pipe bursting costs marginally more than pipe lining, but is well worth its price tag since digging up driveways or sidewalks is avoided entirely. It’s the only way to fully replace damaged pipes without intensive digging.
Can’t Afford Orangeburg Piping Replacement?
While replacing Orangeburg piping should be a priority (remember, replacement is going to ultimately be a lot less expensive than cleaning up after a collapse), we understand that immediate replacement is not a financial option for many. Unfortunately, it’s also not often covered by insurance; if your policy does include sewer lines, chances are there is a “cap” on payouts and you’ll still be on the hook for some of the expense. You should check in with them as soon as possible.
In the meantime, have your plumber send a camera down into the sewer every six months to keep tabs on the situation. This costs money too, of course, but perhaps you can share the cost by taking turns with a neighbor or two; it’s likely they have Orangeburg piping that was installed at the same time, meaning it’s probably in similar condition. If their pipes seem to be holding up, then it’s a safe bet that yours are too, and vice versa.
If the inspection reveals damage but no imminent danger, your plumber may be able to extend the life of the pipes a bit longer by snaking them while you look into a loan or other means of affording the replacement.
Out With the Orangeburg, In With the Trenchless
Fortunately, for owners of older homes and properties, trenchless technology offers an ideal solution to the problems created by deteriorating Orangeburg sewer pipe. By eliminating the need to physically dig out your damaged pipes, you keep labor to an absolute minimum and avoid any costly, stressful landscaping renovations. This lining application is ideal for virtually any type of pipe damage, whether it’s cracking due to temperature change, fracturing at critical pipe joints or deterioration with age (often the case for Orangeburg pipe systems).
By using trenchless technology to reinforce, reline, and restore your Orangeburg sewer pipe line, homeowners can also benefit from using ‘green’ technology, which reduces risks from underground toxins and substances that can arise during conventional pipe restoration and digging.
It is no wonder why this highly efficient and effective method of pipe repair has become so prevalent today. The integration of trenchless technologies with deteriorating or damaged Orangeburg pipes is now one of the simplest and most beneficial methods of Orangeburg restoration.
While Orangeburg sewer pipe served its purpose in assisting the war effort, it’s a bad idea to keep it around in its current state. Otherwise, it will just continue to collapse until it causes you a problem. If you’re aware that you have Orangeburg pipe, then it will pay you to get it lined up as soon as you can. For the best long-term sewer pipe care, homeowners should take an active stance to repair the aging pipes before full collapse. If you think your aging Orangeburg pipes may be starting to fail, don’t hesitate to contact a trenchless plumbing expert in your area.
What is PEX Plumbing?
PEX piping or cross-linked polyethylene is a type of flexible piping that has been gaining popularity recently. As an alternative to copper and galvanized piping, PEX synthetic piping is a favorite among DIYers and in new construction projects.
We’ll explain how PEX plumbing is used and go over the pros and cons for you.
PEX Piping 101
Cross-linked polyethylene was invented in the late 1960s and started appearing in homes and new construction in the U.S. in the ’80s and ’90s. First used for radiant floor heating, PEX quickly became popular due to its price, performance, and flexibility.
PEX is unique because it’s produced by linking polymer molecules in polyethylene which increases its flexibility and durability.
PEX pipe manifold in new construction
PEX Pipe Advantages
There are many benefits of PEX piping, including:
- Lower cost to install. PEX costs roughly the third of the price that copper piping costs. And if you’re looking for whole-home piping in new construction, the cost savings can really add up. Also, the price of copper varies in different markets while PEX is less prone to price changes.
- Corrosion resistance. Unlike galvanized steel pipes and copper piping, PEX is resistant to corrosion, mineral buildup, and erosion.
- Ease of installation. For many minor DIY projects, it doesn’t require a plumbing license to do your own PEX pipe installation (although there are special tools). For example, one can replace old pipes in a leaky sink. Since PEX is flexible, it allows for easy installation in hard to reach places.
- Efficiency. PEX pipes have a smaller diameter than other types of pipes, so the wait for hot water is shorter, resulting in less waste of water. Additionally, PEX material has greater thermal conductivity properties than other types of pipes which reduces heat loss.
- Quiet operation. You won’t have to worry about pipes rattling with PEX since they are made out of synthetic plastic.
PEX Pipe Disadvantages
- Installation errors. While some people may find PEX installation to be easy, others may be in over their heads. We recommend leaving pipe installation up to the professionals, especially if it involves more moving parts, running lines from other rooms, or in brand new construction.
- Heat damage. PEX is susceptible to failure in high-heat situations so it cannot be installed directly to water heaters (although there are connection materials to workaround). It also cannot be placed near recessed lighting.
- UV light. PEX is very sensitive to UV light, so it’s important that all PEX piping be hidden from direct sunlight and UV light bulbs. Many manufacturers recommend total darkness for PEX pipes so this limits where it can be installed.
- Chemical issues. Some types of PEX have been known to leach toxic chemicals like BPA and other contaminants. PEX can also be damaged due to high levels of chlorine in the water. Always have your water tested before PEX installation to see if it’s suitable to use.
- Permeability. Since PEX is plastic, there’s a likelihood of damage, and rodents can even chew through the pipes. PEX is not suited for outdoor installation or exposure to elements. PEX is permeable which means liquids can enter the pipe.
Plumbing Vents
We depend on indoor plumbing, so plumbing problems can disrupt our households. Learn what issues can cause your vent pipes not to work properly and what to do.
Why Does My Home Need Plumbing Vents?
Most homeowners will encounter a plumbing issue now and then, but diagnosing the problem involves more than just checking the water pipes. Plumbing vents can also become clogged or damaged, causing stoppages and a host of other issues. Understanding this sensitive part of your plumbing system is important in order to keep the drains flowing smoothly in your home. We’re here to provide answers to some of the most common questions homeowners ask about plumbing vents.
What Exactly Is a Plumbing Vent?
The plumbing vent, also known as a vent stack, helps regulate the air pressure in your plumbing system. Just as drain pipes remove water and waste from your home, the plumbing vent pipe – also known as a plumbing air vent – removes gas and odors. It also allows fresh air into the plumbing system to help water flow smoothly through the drain pipes. However, no water runs through the plumbing vent pipe. It is a vertical pipe attached to a drain line and runs through the roof of your home. The vent stack is the pipe leading to the main roof vent. It channels the exhaust gasses to the vent and helps maintain proper atmospheric pressure in the waste system.
Why Are Plumbing Air Vents Important?
Your home’s plumbing system is designed to efficiently remove water and waste. Its drainage and vent functions are actually two systems that work together.
Drainage pipes carry waste out of your home to either the city sewer or a septic tank. Vent pipes supply fresh air to each plumbing fixture in the house, which helps the system move water through the drainage pipes each time a toilet is flushed or a sink is drained.
Plumbing air vents also prevent sewer gasses from entering the home and allow wastewater gas and odor to escape. Plumbing vent pipes are located on roofs, away from windows or air conditioning units, so that the fumes can easily dissipate.
How Can I Fix Problems with Plumbing Vent Pipes?
When plumbing air vents or vent stacks do not work properly, neither will your home’s plumbing drainage system. If you hear gurgling sounds coming from your drains, see standing water in your sink or bathtub, or notice a slow drain in the bathroom or kitchen, a blocked vent may be the issue.
When a plumbing vent pipe or vent stack is blocked, negative pressure builds up in drainage pipes and water flow is interrupted. Though you may have success clearing a clogged drain yourself, stoppages will continue to occur if a blocked vent is the culprit.
Ongoing stoppages and slow-flowing drains can lead to sediment forming inside the drain pipes. This can further damage your plumbing system and may result in hefty pipe repair or replacement costs down the road.
If you can’t clear a slow-flowing drain with a plunger, auger or drain cleaner the vent blockage may be severe. If the plumbing air vent or vent stack becomes completely blocked, a vacuum will form, and you will no longer hear gurgling. You will also be able to smell sewer gasses in the rooms where the affected fixtures are located. This is a problem that requires immediate attention from a plumbing professional.
American Home Shield warranties cover a variety of plumbing issues, offering peace of mind when it comes to one of your most important investments – your home.
Polybutylene Piping

Polybutylene (PB) was a plastic manufactured between 1978 and mid-1995 for use as piping in home plumbing systems. It was inexpensive and offered plenty of advantages over other materials, such as flexibility, ease of installation, resistance to freezing. Pipes made from polybutylene were installed in up to 10 million homes in the United States during that period. Despite its strengths, production ceased in mid-1996 after scores of allegations surfaced claiming that polybutylene pipes were rupturing and causing property damage. In the homes that still contain this material, homeowners must either pay to have the pipes replaced or risk a potentially expensive plumbing failure.
How Does Polybutylene Fail?
Two studies in particular in papers published by the University of Illinois at Chicago have shown that certain disinfectants can react with the polybutylene and cause it to flake apart at any location within the PB piping system. Small fractures can deepen over time and eventually work their way to the pipe’s exterior, allowing water to escape. Some manufacturers, however, claim that the majority of leaks occur at joints and unions, which is where a leak would likely appear if a pipe were improperly installed. Despite this contention, class-action lawsuits filed against PB manufacturers have been successful and resulted in payouts to homeowners reaching $1 billion.
Polybutylene Pipes Should Be Replaced
Although no regulations require the replacement of polybutylene piping with other material, many plumbers recommend doing this, at a cost several thousand dollars. Leaking can happen without warning and can result in flooding and serious damage to a home’s interior if it is not immediately stopped. PB pipes installed behind sheetrock can leak unnoticed for long periods of time and cause mold and water damage. InterNACHI believes it is far cheaper to replace polybutylene pipes before they fail and release their contents onto floors, appliances and furniture. They can also reduce a home’s value or prolong its time on the market. Homeowners might face higher insurance premiums or be denied coverage entirely. For homeowners who are concerned about this problem and wish to replace the PB piping in their home with copper or other material, there are companies that specialize in this type of work.
Identifying Polybutylene
An inspector can use the following tips to identify polybutylene plumbing. Polybutylene pipes are:
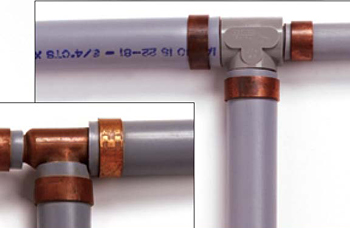
- usually stamped with the code “PB2110”;
- flexible and sometimes curved, unlike rigid piping materials such as copper;
- not used for waste, drain or vent piping;
- most commonly gray in color, but they can also be white, silver, black or blue. Blue PB is used primarily outdoors and should only be used to carry cold water. Inspectors should be aware that black or white pipes might not be polybutylene (they might be polyethylene or PVC, respectively). Also, PB color is somewhat region-dependent. For instance, experienced home inspectors in California might never come across gray PB, while it is quite common elsewhere;
- ½” to 1” in diameter.
Polybutylene pipes can be in a home’s interior or exterior in any of the following locations:
Interior:
- protruding from walls to feed sinks and toilets;
- running across the ceiling in unfinished basements;
- near the water heater.
Exterior:
- entering the home through the basement wall;
- at the water meter;
- at the main water shut-off valve.
Note:
- Home inspectors are not required to note the presence of polybutylene, and no tests for weaknesses should be performed. Any deterioration of polybutylene pipes happens from within and cannot be detected without turning off the water and dismantling the pipe, which is far beyond the standards of practice of home inspection.
- Inspectors should check an entire pipe for PB, not just a portion of it. Some copper piping systems have been found to use PB at junctures. A common example of this union is where PB pipe links with copper “stub outs” that feed bathroom fixtures.
Other piping materials not to be confused with PB:
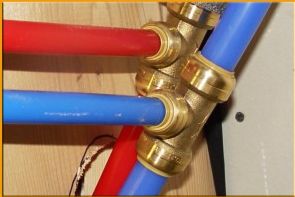
- PEX (pictured at right): Common in radiant-heating systems, this cross-linked polyethylene can be black, blue or red. It is more easily coiled and more flexible than PB. It can withstand higher temperatures than polyethylene.
- PVC: A popular building material commonly used in residential plumbing. CPVC is derived from PVC and is also used in plumbing. Both appear white or off-white and can be flexible or rigid.
- Polyethylene: This material is flexible and black.
- Copper: Copper is a metal that should never be confused with PB.
If in doubt, a licensed plumber can be contacted to determine whether or not a pipe is made from PB.
PVC Pipes
:max_bytes(150000):strip_icc():format(webp)/types-of-pipe-used-for-water-2718736-03-d4fc008f7ea346169480a21d3a164b42.jpg)
PVC is an acronym that stands for polyvinyl chloride. Of the different types of plastic pipe used for water supply, PVC pipe has a wide variety of plumbing uses but is mostly used for drainage PVC is rarely used in potable water applications, and in many jurisdictions it is not considered safe for drinking. PVC is also very common in pool and spa systems. PVC pipe is often white but it can also come in other colors. You can often tell what it is used for by the colors and marks on the pipe. For example, purple pipe with black lettering is sometimes used for reclaimed water. PVC also comes in a variety of thicknesses, called schedules. Schedules 40 is common for pipes used in water distribution.
PVC Piping Uses & Applications
PVC piping is used for:
- Drain-waste-vent (DWV)
- Sewers
- Water mains
- Water service lines
- Irrigation
- Conduit
- Various industrial installations
It can be used under ground or above ground in buildings. It can also be used outdoors if the pipe contains stabilizers and UV inhibitors to shield against ultraviolet radiation and it is painted with a water-based latex paint.
PVC materials are resistant to many ordinary chemicals such as acids, bases, salts and oxidants.
Because PVC piping system components can be manufactured in a variety of colors, identification of application is easy. A common color scheme (although not universal) is:
- White for DWV and some low pressure applications
- White, blue, and dark gray for cold water piping
- Green for sewer service
- Dark gray for industrial pressure applications
This color scheme has an exception in that much of the white PVC pipe is dual rated for DWV and pressure applications.
PVC piping systems should not be used to store and/or convey compressed air or other gasses. PVC piping systems should not be tested with compressed air or other gasses either.
PVC piping is recognized as acceptable material for DWV, sewers, and limited potable water services and distribution in all model plumbing codes. These Codes normally identify acceptable products for specific uses based on the ASTM Standard designation. Exposed PVC (plastic) used above ground to distribute water through the residence may be subject to UV damage from the Hawaii’s extra strong sun and the potential for degredation and or damage to the pipe is moderate to high. We recommend replace, update or upgrade or consult an expert for more information
Sewer Pipe Sagging Or “Belly”
Sewer line bellies are a common problem that can create aggravating sewer pipe problems for property owners. A sag in a sewer pipe will eventually lead to standing water and sediment collecting in the middle of the line, which in turn can lead to erosion, blockages, and a major backup for the homeowner.
What Is a Belly in a Sewer Pipe?
Sewer line bellies are sags or low spots in sewer lines. A normal sewer lateral (seen below) has a slope that uses gravity to help regulate the flow. A bellied sewer line interferes with the normal flow of waste water through the pipe, leading to backups and other problems because the water and sediment collects in the belly.
What Causes Sewer Bellies?
Poor planning and bad installations are often the root cause of sewer line bellies, as proper bedding compaction, good materials and correct slope are the most important factors needed to prevent the problem. However, natural occurrences like major tree roots, earthquakes, sun or heat, rain, and even cold weather fluctuations can lead to the shifts in the soil that eventually cause bellies.
To prevent bellies, the first step is to install plumbing with proper bedding. If the correct material (larger grade gravel and sand) is not used under the pipe, then it may eventually settle lower into the ground in some sections and a belly will form.
A sewer line must also have the correct slope in order to use gravity to its advantage when moving waste away from the home or building. A trenchless professional will use the best tools of the trade (such as video cameras and locator wands) to ensure proper slope in a plumbing installation thereby preventing excess build-up.
In some cases, unstable ground may cause bellies, too. Even sewer lines that have been installed with the appropriate support in place may sag if the earth below begins to shift.
Sewer Cleanout Location: Where is My Sewer Line Cleanout Located?
by The Original Plumber | Oct 25, 2020
A sewer drain cleanout is an essential feature of the drainage pipe system in your home. If a sink or a toilet is causing a blockage of the system which results in the sewage backup, then the cleanout is the only interface through a plumber that can unravel the mess. While a professional plumber can quickly locate the sewer line cleanout in many homes, the homeowner should stay aware of its location for emergencies. Note that the authorities usually take care of the main sewage line in the neighborhood but leave your compound’s systems under your care. Therefore, you should know the “sewer safety valve” location as it can help you remove obstructions on the system and avoid the dirty seeping on your floor.
How the sewer line cleanout works
A sewer line is a large pipe that connects every sink, shower, and toilet in your house to the municipal sewer line in the city. If one toilet, sink, or other facility causes a block on the septic line, all other facilities are affected, which calls for immediate action. Unblocking the sewer system is easy if you have a sewer cleanout in the house or the compound. Note that the service fee for unblocking the waste disposal system will partly depend on how easily a plumber can access it; you pay higher if there is no cleanout or don’t know its location.
Typically, a sewer drain cleanout is a sizable threaded pipe ending with a plug. The tube can either be metallic or plastic depending on factors like the area of residence and the weather. Moreover, its house or compound location is also influenced by factors like the weather and the house’s materials. For instance, homes in localities that experience cold weather often have sewer cleanouts near the bathroom, toilet, or garage.
Where is my sewer cleanout located?
A homeowner has various options when they need to find the cleanout. A sewer cleanout is a safety feature among the utilities. One should always know their location from the day they move into a house. However, it is easy to identify the cleanout, and sometimes you do not need professional help. That is not always the case since there are times when the cleanout is buried in the compound. Here are the various ways to locate a sewer drain cleanout.
- Examine the likely locations –The first way involves looking around in the house and the compound in places where you would expect the facility to be installed. A cleanout is a 3- or 4-inch pipe fitted with a screw cleanout cap, and it is easily identifiable. Therefore, looking around the compound is one way to determine its location. In most homes, the cleanout is located close to the bathroom, either inside or outside the house. However, this is not always the case, and your neighborhood may be different. Therefore, you should not panic if you do not find it anywhere near the bathroom. Other probable places to check include the garage area, in the basement, or near the pathway right outside the house. If the sewer cleanout access is located in drywall, you should take care and avoid cutting other pipes, cords, and cables, or you could cause a tragedy in the home.
- Grab the house plan – Sometimes the eyes may not be enough to tell where the lateral sewer line cleanout is located. In such a case and where the house plan is readily accessible, it is plausible to get it and try finding the facility from there. The advantage of using the plot plan is that all other features and facilities are documented in it, making it easy. Identifying your house’s sewer line is the first step to locating the sewer drain cleanout. Take care and avoid confusing other facilities with the main sewer line as this may have adverse effects if you damage other systems in the process. As mentioned before, the sewer cleanout could be buried in the compound instead of located inside the house.
- Professional services – In some cases, observing the compound and looking at the plot plan does not yield any results. This could be the case for old houses or those whose plans are poorly done or the case of a buried sewer cleanout. Therefore, calling a professional service may be the only option. You can quickly locate the outdoor cleanout access with expert help regardless of whether it is inside the house, sticking out, or buried in the compound. Plumbers have the tools and expertise to trace, replace, and repair parts of a drainage plumbing system. Whether that’s using a modern technique called trenchless sewer repair or using a variety of other ways to unclog your sewer, you can always be confident with their expertise. They can also discern why your drainage system is often clogging and give you professional advice on the same. Furthermore, professional plumbers will cause little or no damage when finding the sewer cleanouts. Even better, a plumber may fix any damages caused on some walls if the sewer cleanout was underneath one. One other advantage is that a plumber can install the lateral sewer line cleanout if there is none in the compound. And even though this adds to the service cost, it is well worth it unless you will be moving out of the house the same day.
Taking care of the drainage system in your house
What can you do to prevent the drainage system from clogging? You know the pain of dealing with a clogged drainage system if you ever experienced one. For people who are yet to, you’d better take precautionary measures before it is too late. Below are some practices that can prevent or reduce clogging of the drainage system in your home.
- Use hot water frequently – Hot water is known to kill germs but is also a remedy for clogging pipes as well. Cleaning the sinks with boiling water melts out oils and detaches food items from the pipes’ walls, thus getting them into the street’s central sewage system. Therefore, you should make a point of cleaning the sinks, bathrooms, and toilets with hot water frequently.
- Use a drain guard on every sink – In some instances, the drainage pipes will block because too many food items find their way in the lines. Having a drainage guard on every sink in the house reduces the size and amount of foodstuffs entering the drain. With this tip, you will also need to avoid dumping non-dissolvable waste in the sink or bathroom.
- Do NOT use chemicals to clear clogs. Chemicals are harsh and can easily damage your pipes. Additionally, these chemical will harm reefs and marine life
- Routine maintenance – Routine maintenance is the best way to stay out of trouble with drainage systems. Every homeowner should ensure that the drainage system is inspected by a professional plumber at least once a year. Possible problems that then be identified and resolved before the drain blocks. This does not only save you money eventually, but it also ensures your system is in the best condition at all times.
Conclusion
Knowing the location of the sewer cleanout in your compound is of great importance. Besides helping you reduce the cost of sewer line repairs and maintenance; it can help you keep the drain clean through DIY activities and regular inspections. Most houses have the sewer drain cleanout on the inside near the bathroom. If you cannot find the sewer cleanout by observing the house and the compound, then looking at the house plan or calling a professional plumbing service could be the salvation.
Above all other things, it is vital to keep the drainage system clean and healthy at all times.
Sewer Scoping
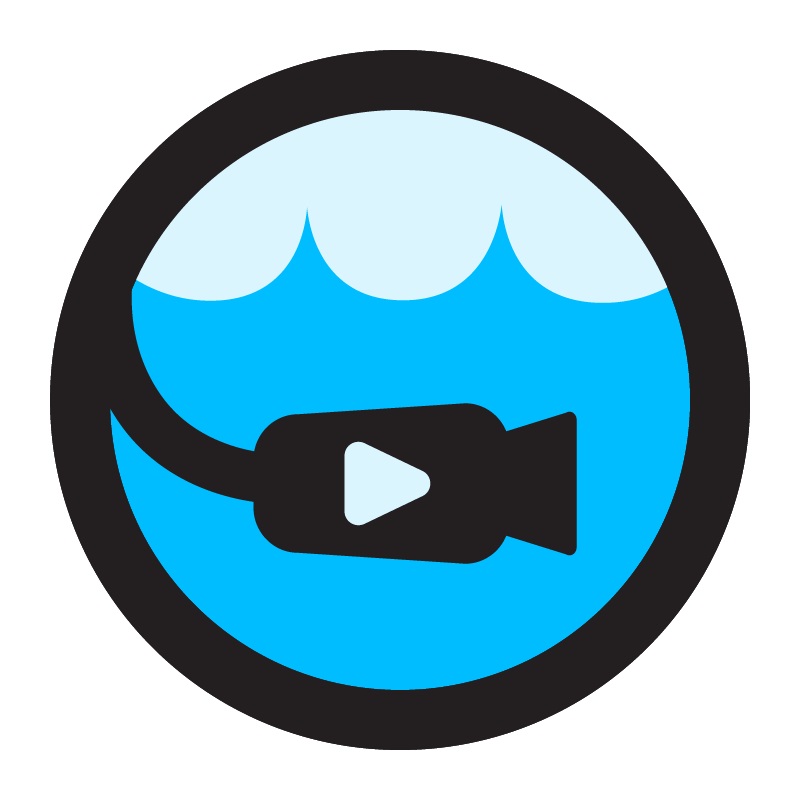
About Sewer Scope Inspection Process
List of Scopers
Having a sewer scope inspection performed usually only takes a few minutes – and the inspection is just what it sounds like. A trained, professional plumber will run a specialized, flexible borescope camera, which feeds images and video to a monitor. Then, this camera is run through your home’s drainpipe, to examine the sewer lines and other underground pipes for any flaws, imperfections, or serious problems.
The entire process usually takes no more than an hour, altogether. After this, your plumber will tell you about their findings, and issue a report that’s given to you with information about the condition of the sewer line.
Sewer Scope Inspection Cost
The cost of a sewer scope inspection will vary based on the area in which it’s performed, the specifics of the house, the inspector you use, and a number of other variables. However, it’s quite affordable, in most cases. The cost will tend to vary from $250-$500.
This may seem steep. However, consider this – the cost of repairing a broken sewer line costs around $300-$400 – per foot of repaired line. Repairing and replacing an entire sewer line or a line with major structural faults could easily run you thousands of dollars.
Should I Get A Sewer Scope Inspection?
Absolutely. As touched upon above, a sewer line is often one of the most costly things to repair in a home. Getting a sewer scope inspection can help you avoid investing in a home that has serious issues with the sewer/septic system.
You may even be able to save a bit of money on a sewer scope inspection if you’re able to find a home inspector who offers this service along with other traditional home inspection services, such as lead and asbestos inspections. Bundling these services usually will allow you to get a better deal.
Signs You Should Get A Sewer Scope Inspection For Home Purchase
Cracked Sewer Line
Before you go looking for a home, it’s a good idea to know what to look for, and what signs may indicate that you must get a sewer scope inspection before making an offer on a house. Here is a short list of some of the most common signs that something may be wrong with the sewer system, or that it’s at risk of being damaged.
- Water backing up inside the house or crawlspace – This could indicate damage or breakage to the sewer line, or a significant clog.
- Large trees in the yard – One of the most common causes of sewer pipe damage is the growth of roots around the pipe. Roots can grow around and constrict the pipe, breaking it, or grow into small cracks in the pipe, clogging it or causing leaks.
- The house was built more than 30 to 50 years ago – Homes built before 1984 may have clay sewer pipes, which can be easily crushed or damaged. These typically must be replaced, or at least inspected to ensure that they are in good condition.
- You notice shifting or movement of the ground around the home – If the soil around a house seems to have shifted, the pipe may have been affected. If it has moved, it could have broken or become bent and damaged, which may require a costly repair. |
To identify this, look at things like the sidewalk and driveway. Are the surface soils level with the driveway or walkway? Do they seem to have sunk, or become piled higher than these concrete surfaces? - Extra-green or lush patches of grass – This is a common sign of a septic or sewer leak. Given its contents, sewer water is actually a powerful fertilizer that can help encourage plant growth. If you see a suspiciously healthy-looking area of the yard, especially if the rest of the lawn seems to be less lush or green, you should be suspicious.
Even if you don’t see any of these above issues, we would still recommend a sewer scope inspection. More minor issues with the sewer line may have few or no symptoms at all – but still cost thousands to repair.
Sewer Scope Inspection Results – What To Look For
Wondering what to look for during the inspection? You’ll typically watch the video feed throughout the process. You and your inspector will be looking for:
- Serious clogs or blockages in the sewer line
- Cracks, damage or imperfections in the line
- The type of material used for the line (clay, concrete, plastic, metal, etc)
- Roots growing through the line
- Separation or failure of the line
- Potential damage or issues with the septic tank (if present)
Your plumber should walk you through the entire process, and help you understand what you’re seeing. If no issues are detected, great! If there are some minor problems, you may be able to negotiate a better rate on the home, or at least plan for the repair in your home budget during the next few years. Finally, if there is a major issue, you likely will be able to walk away from the sale, require the homeowner to make the repair themselves, or get them to reduce the cost of the property accordingly.
Know Before You Make An Offer: Get A Sewer Scope Inspection!
Need to find a reliable home inspector for a sewer scope inspection? Here are some trusted vendors…
Licensed Plumber, Pueo Plumbing, 808-593-PUEO, Josh Stamm, Owner, License #C-34564, Pipe Scoping, Plumbing, Drain Service & Sewer Repair
Licensed Plumber, Commercial Plumbing Inc., License C-13503, Pipe Scoping, i@complumbing.com, (808) 845-4112 1820 Colburn Street, Honolulu, Hawaii 96819
Licensed Plumber, EverTrust Plumbing, Nathan Herm, Master Plumber, Pipe Scoping, evertrustplumbing@gmail.com, www.evertrustplumbing.com, (808) 841-9649 730, Mo’owaa St, Ste E Honolulu, Hawaii 96825
Licensed Plumber, Lic #C-34399, Pipe Master Plumbing, Devin Watabu, Service Technician, Pipe Scoping, Pipe Cleaning, Pipe Relining, Pipe Bursting, Pipe Coating, info@oahupipemasters.com, www.oahupipemasters.com, (808) 396-PIPE (7473), 820 W. Hind Dr., Honolulu, Hawaii 96824